Digital construction combines efficiency and sustainability
The construction industry: a bumpy road ahead
According to Statista, the German construction sector reported continued growth in turnover up until 2019. The industry was even able to defy the pandemic. Nevertheless, the outlook forecast by the Federation of the German Construction Industry is rather subdued. The main reason behind this is the shortage of materials. There isn’t enough wood, concrete, metal, steel or petroleum, and this is sending the costs of raw materials spiralling. Another challenge is climate change because the construction industry is resource- and energy-intensive. Research by the non-profit organisation World Green Building Council indicates that a good 40 per cent of global carbon dioxide emissions are generated by construction. Producing concrete is the main cause, as this involves firing limestone. For the energy transition to succeed, the construction industry also needs to become more sustainable. But how can we maintain the construction boom of recent years while protecting the environment?
This is exactly where digital construction comes in. With the aid of artificial intelligence (AI) and robotics, the construction trade could become more sustainable – from the first draft of the plans to handing over the keys to the new occupiers.
Digital construction begins at the planning stage
Whether the project is a private residence or a housing complex, constructing a building requires many steps and involves numerous companies. From the architects’ practice to the cement factory, everything is interconnected. Right from the initial plan, the structural engineering, suitable materials, building regulations and energy efficiency need to be taken into account.
Computational design can help to further optimise the planning of construction projects. CAD (computer-aided design) has been the industry standard for a long time. But modern software goes beyond this by applying AI. The foundation for these solutions is the enormous databases that are used to train algorithms and set rules. This means that accurate models can be developed, assembly drawings produced, and lists of the required materials generated automatically. It’s an approach that saves raw materials, shortens the construction time and cuts costs.
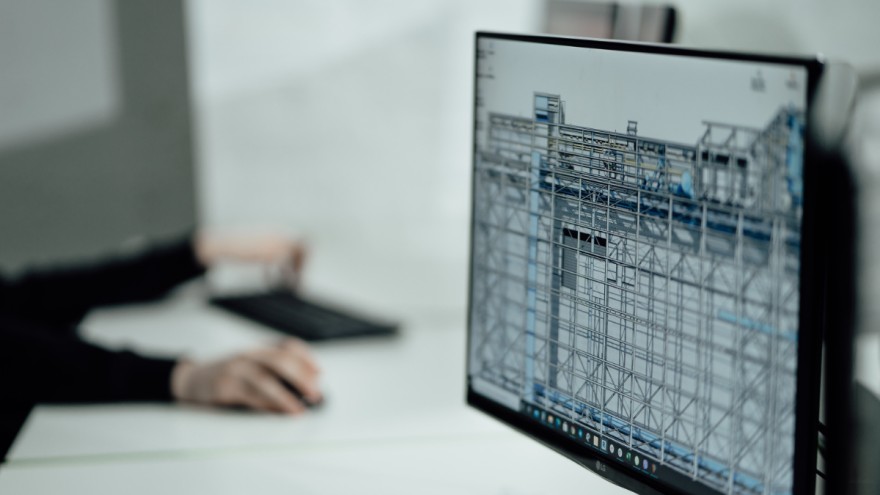
CAD software can be used to generate 2D drawings and 3D models. (Photo: Evgeniy Surzhan on Unsplash)
Machine learning: always a step ahead
Algorithms are trained with the aid of databases. To improve their performance even further, machine learning is used. Machine learning enables algorithms to analyse data and enrich their knowledge independently. In this way, they can make decisions and provide forecasts that have an even firmer grounding – something that could benefit the construction industry greatly.
This is precisely what the University of Stuttgart is currently researching. The idea is to simulate models that factor in very different influencing parameters and their mutual dependencies in a virtual solution space. Model-based algorithms that apply machine learning can run through vastly different scenarios at the speed of seconds. For instance, they can calculate the ideal shape of a high-rise building in relation to wind load or a building’s optimal energy consumption.
Hard-working robots in construction
What would the future look like if we had alternative raw materials or processes that allowed us to build more resource-efficiently? In fact, a whole range of innovative materials and processes already exist. Furniture made from hemp fibres and bamboo as a construction material are just two examples. Now even replacement parts for household appliances and furniture are produced with 3D printers . And then there’s modular construction, a process for constructing buildings from individual components. This speeds up the construction process, generates less waste and simplifies repairs, among many other benefits.
Robots can produce alternative construction materials and modules based on computer-generated models. This process is called digital fabrication. Researchers working on a joint project by the Universities of Stuttgart and Freiburg have built the livMatS Pavilion , which consists of robotically wound flax-fibre elements. Flax is a regional plant that is 100% biodegradable, regulates air humidity and the temperature, and repels dirt. With the aid of a coreless winding process, the robots are able to produce very lightweight yet robust construction components from the fibres. Another example is the DFAB HOUSE by ETH Zurich. The research building was both digitally designed and built with the aid of flexibly deployable robots and 3D printers.
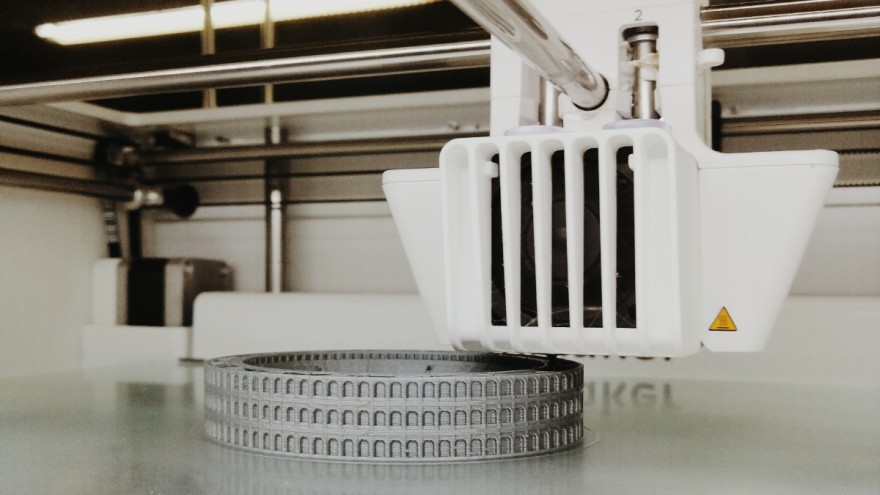
Digital fabrication: 3D printers can produce replacement parts and even complete components. (Photo: Andrea G on Unsplash)
Resource-efficient construction and homes
Shortages of materials, climate change and population growth are placing the construction industry under mounting pressure. Digital construction has the potential to transform the industry and tackle these challenges effectively. From AI algorithms to accurate model development and digital fabrication with robots, numerous projects show us what the construction industry of the future might look like. And the same goes for interior design. Growing numbers of companies are devoting themselves to sustainable furniture production by adopting modular systems, alternative materials and digital technologies, among other approaches. All this takes us one step closer to completely sustainable homes tomorrow.