“Green” fabrics – creating wonders from waste
PET felt – a 100% recyclable moulded non-woven fabric
Environmentally friendly, functional, sound-absorbing, soft to the touch, versatile ... PET felt boasts countless useful properties, so it’s no wonder that the textile is becoming increasingly popular. It combines sustainable design with a wide range of colours and potential applications. Having been used for many years in ceiling elements, wall panelling, partition walls and lighting solutions, the material has now been embraced by the furniture industry as well.
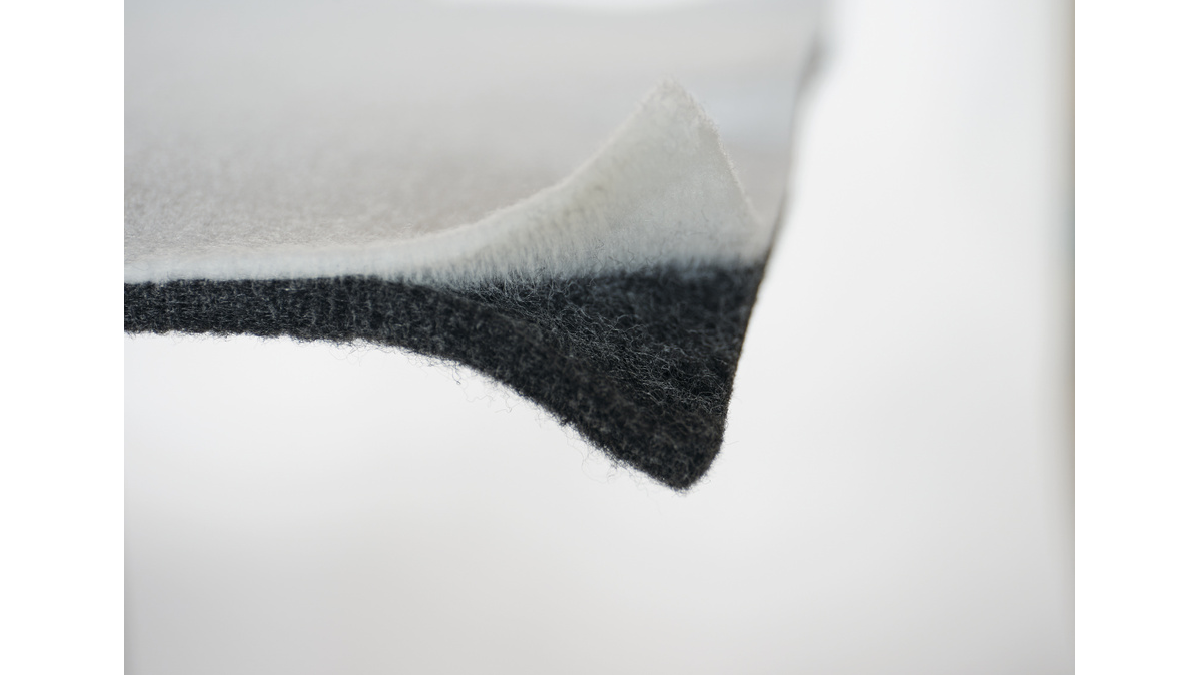
PET (polyethylene terephthalate) felt is made from recycled plastic bottles. The non-woven fabric can be repurposed or recycled after use, significantly extending the life of the material beyond its original application. Copyright: Klöber
German seating furniture manufacturer Klöber has launched an entire family of products featuring PET felt. In the WOOOM range, the seat shell of the lounge armchair, the low-backed bucket chair and the meeting room chair is made from a moulded non-woven material. “Sustainability isn't a mega trend for us, it's just how we rock”, says Thomas Möller, CEO at Klöber. “With every new development, we strive to reduce the percentage of virgin materials in the design to the bare minimum and to use as much high-quality recycled material as possible instead. PET felt is made from recycled plastic bottles. With an almost infinite supply of reusable materials available, it is an important step towards preventing single-use plastic bottles from reaching landfills and our oceans. While using the material doesn’t solve the problem entirely, we are making a small contribution – and we’re proud to do so.”
PET felt is 100% recyclable. It contains up to 60% polyester fibres that are recovered from bottle flakes, i.e. shredded PET bottles, 100% of which Klöber sources from countries in Europe
Leap – imitation leather made from apple leftovers
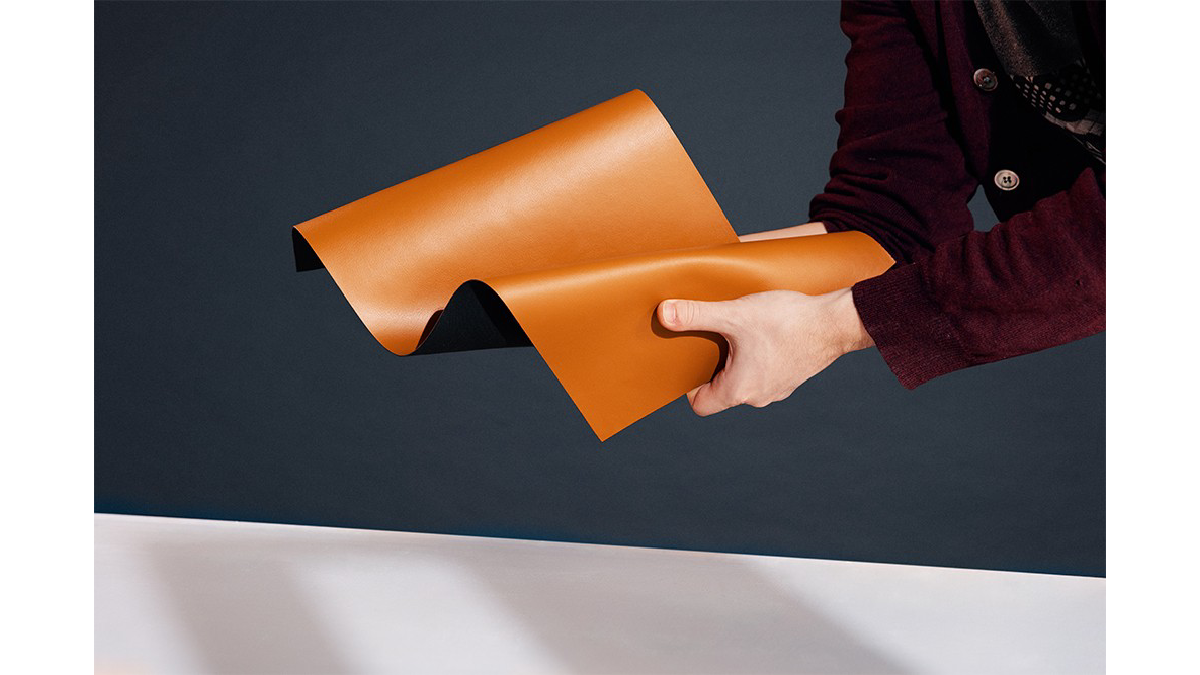
The name Leap is short for “LEftover APples”. It’s a vegan-certified next-generation fabric containing 89% bio-based materials. Copyright: Beyond Leather Materials
Apples are popular snacks: as well as being healthy, they’re easy to eat and can be slipped into almost any pocket or bag to enjoy on the go. While around 75% of the world’s apples are eaten as they are, around 25% of the crop is processed to make juice, jam and other foods. It’s estimated that some 3,000,000 tonnes of apple scraps are thrown away every year. Danish start-up Beyond Leather Materials finds this situation unacceptable. But what can you make out of apple leftovers? Imitation leather, of course!
The initial idea formed quickly, but the journey to realise the final product was a difficult one. Working with engineers from KEA, the Beyond Leather Materials team developed a leather-like fabric, which they called Leap, a name that is itself derived from “LEftover APples”. Leap is made from recycled apple waste, natural rubber and other bio-based ingredients. “In using apple pulp, we want to make a positive contribution by helping producers of apple juice and cider to reduce their waste costs and prevent apples from being dumped in landfill sites,” explains Mikael Eydt, co-founder and CEO of Beyond Leather Materials. “This approach allows us to create an innovative alternative to animal-based materials.”
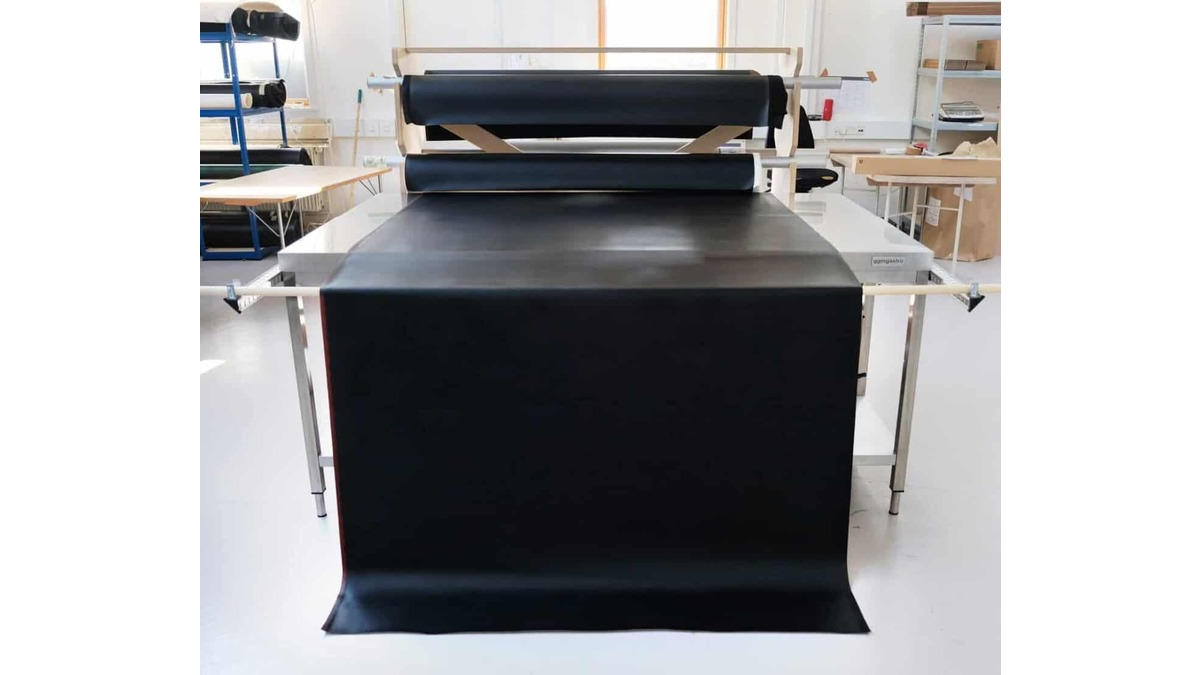
Important step forward: in May 2024, the team from Beyond Leather Materials opened the company’s first full-featured roll-to-roll production line in Germany. Copyright: Beyond Leather Materials
In May 2024, Beyond Leather Materials took an important step forward when the team opened its first full-featured roll-to-roll production line in Germany. “Almost seven years of product development and extensive research have led us to this critical moment,” says Eydt. “Leap represents a shift in the way we think about and utilise waste by transforming discarded materials into valuable resources. The product is an example of how we can take another step towards a more carefully considered approach to the use of materials in industries that often rely on animal-derived inputs or standard plastics.”
Seawool – a yarn made from oyster shells
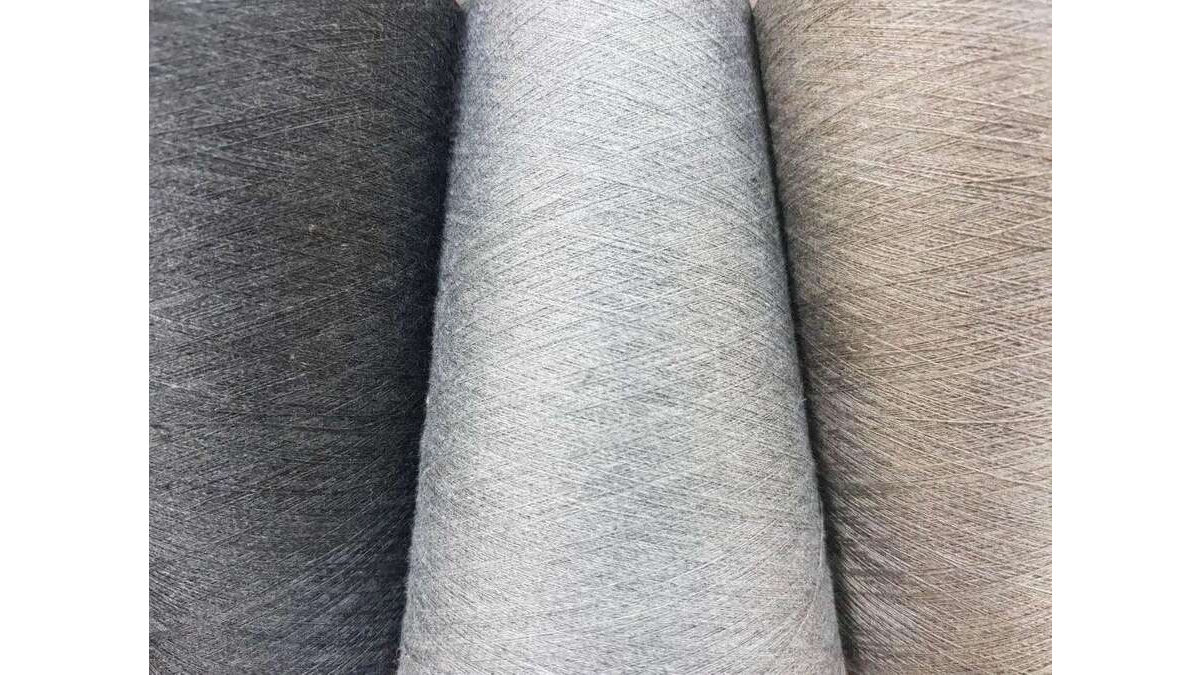
Seawool is the latest sustainable yarn developed by Creative Tech Textile and launched on the international market in collaboration with Hans Global. Copyright: Creative Tech Textile
There is a long tradition of oyster farming in Taiwan, where they have harvested the shellfish in significant quantities for over 300 years. However, the surprisingly large volume of shells discarded by the industry has previously been largely ignored. In Taiwan alone, oyster farming produces more than 160,000 tonnes of waste shells each year – and they don’t decompose. Although some of the oyster shells are used to make soil improver or food pellets for livestock, the problem has not been solved.
After years of research, Creative Tech Textile has now succeeded in developing a method of spinning the discarded shells into a yarn: Seawool. The shells are ground into a fine powder and combined with thread made from recycled plastic bottles. At the end of the production process, a material is created that boasts some of the natural properties of discarded oyster shells. It feels like wool, retains heat and is naturally odour-inhibiting, antibacterial and anti-static – all without any chemical additives.
The Seawool fibre is already being used in the fashion industry, and the first designs made from the yarn are available to buy.